The Health and Safety Executive (HSE) has published a new research report examining the causes of welding-related incidents and failures over the past 15 years. A total of 47 incidents in which welding was considered to be deficient, leading to a failure, were included within the study.
The failure of welds can have a wide range of consequences, including the collapse of structures leading to injuries and fatalities. HSE research found that 49% of failures lead to structural collapse, 21% led to injuries, and 11% led to one or more fatalities.
The research found that the most common types of failure were fatigue and ductile or brittle failure due to the overloading of welds.
Using a root cause analysis, the most common root causes of failures were identified as follows (more than 1 cause can apply to one failure):
- A lack of adequate welder supervision—26% of cases
- Insufficient percentage coverage of inspections—26% of cases
- Joints not having been designed for ease of fabrication—23% of cases
- Suboptimal design of join fit-up – 21% of cases
- Incorrect application/awareness of welding parameters—21% of cases
Overall, the research concluded that the issues relating to welding failures were not focused in a single area but spread across the many stages of welding, including at the design stage, preparation, and the welding process itself.
Full details of the research can be found on the HSE’s website.
If you have any questions or would like support with managing issues at your workplace, please speak to your usual contact or get in touch using the form below.
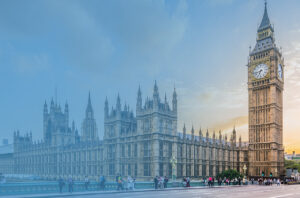
Employment Rights Bill – Government Publishes Implementation Roadmap
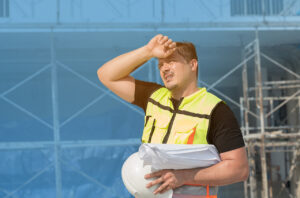
The Sun’s Out – Time To Get The Shorts Out?
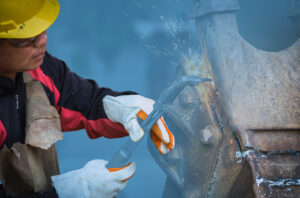
Updated Gas Safety Guidance
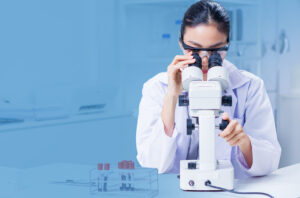
Revised Bloodborne Viruses Guidance
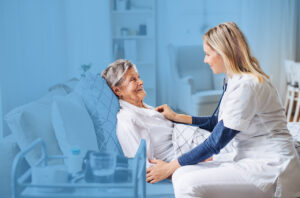
New High Consequence Infectious Disease Guidance for Care Providers
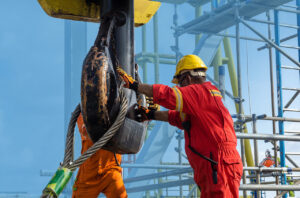